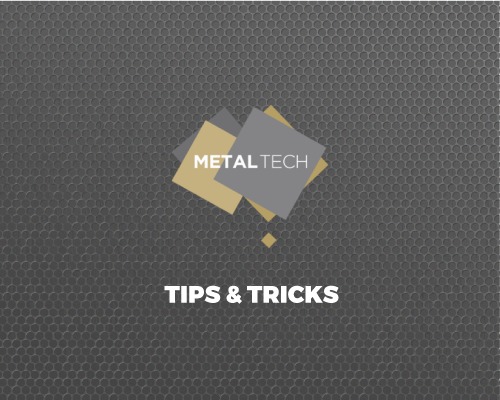
What Are The Advantages of 3D Metal Printing Over Traditional Metalworking?
The difference between traditional metalworking and 3D metal printing is that, in traditional metalworking, objects are created by shaping and molding metals through various techniques such as forging, casting, and stamping. On the other hand, the advantages of 3D metal printing involve using a computer to create a three-dimensional model of an object, which is then printed using a special printer. This printer deposits metal powder layers, which are fused using lasers or electron beams. There are several key differences between traditional metalworking and 3D metal printing, and these differences pose great opportunities for specific occasions and various reasons.
Time is of the Essence in 3D Metal Printing.
The advantages of 3D metal printing process are plentiful. It generally offers a much faster production time compared to traditional metalworking ways. With traditional metalworking, each individual piece must be crafted separately, which can be time-consuming. With 3D metal printing, however, multiple pieces can be printed simultaneously, drastically reducing production time.
The ease of industrial prototyping and the short runs are the main reasons the 3D metal printing process generally offers a much faster production time than classic metalworking methods. The whole process of 3D metal printing is versatile and can be done with different machines, which are specially designed for industrial prototyping. The primary purpose of these machines is to create a three-dimensional object from a digital file.
The industrial prototype can be created within a very short time, which is one reason why 3D metal printing has become popular in recent years. In addition, the production time for short runs is also shorter because it does not require traditional tooling, so the setup time is much shorter. As a result, the total production time is reduced significantly, which offers a faster production time for small businesses or companies without much manufacturing experience.
3D Metal Printing’s Precision is the Key
One of the advantages of 3D metal printing is that it is often more precise than traditional metalworking. This is because the print head in a 3D metal printer can print tiny layers of material (typically around 20 microns). In contrast, most machining tools have a minimum material removal rate that is much larger (on the order of millimeters). This increased precision can be critical for applications where close tolerances are required.
3D metal printing creates three-dimensional objects from a digital file by adding successive layers of material. Traditional metalworking is a subtractive manufacturing process where parts are created by removing material from a larger block or piece of metal.
3D metal printing is particularly well suited for small batch runs and customized parts, whereas traditional metalworking is better for very large-scale production. 3D metal printing could also create medical implants, prostheses, aircraft or vehicle components, and even building structures.
In addition, another one of the advantages of 3D metal printing is that it can be used to produce complex shapes that would be difficult or impossible to create with traditional methods. This allows for greater design freedom and the ability to create parts with unique functionalities. 3D-printed metal parts can also often be repaired or modified more efficiently than traditional ones, saving time and money in maintenance and repair operations.
Conclusion:
In conclusion, the advantages of 3D metal printing over traditional metalworking are predominant. These advantages include creating complex shapes that are difficult or impossible to produce with traditional methods and reduced lead times. Considering these advantages of 3D metal printing, it could rule out metalworking as a manufacturing process for many products, as companies such as Metal Tech have already adapted and improved upon this field. Are there any other benefits you can think of?
Leave a Reply