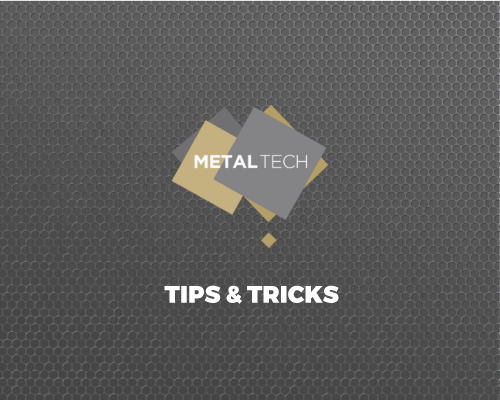
Challenges Of Metal 3D Printing: An Analysis
3D printing is revolutionizing how products are designed, made, and repaired. One of the most popular types of 3D printing is metal 3D printing, which allows for the creation of objects with intricate details that wouldn’t be possible with other methods. While metal 3D printing offers many advantages, it also poses some challenges that need to be overcome to make it more accessible and efficient. In this blog post, we’ll explore the challenges of metal 3D printing and discuss possible solutions. We hope you find this information helpful!
What Are the Most Common Challenges of Metal 3D Printing?
Metal 3D printing holds great promise for the future of manufacturing. However, this technology is still in its infancy, and there are several challenges that need to be addressed before it can truly become mainstream.
High Cost:
One of the most significant challenges of metal 3D printing is the relatively high cost of printers. For a few reasons, metal 3D printers are generally more expensive than their plastic counterparts. First, metal 3D printers require a higher level of precision, which means that they typically have smaller build volumes than plastic 3D printers. Second, metal 3D printers often use powder-based materials, which can be more expensive than filament. Finally, metal 3D printers often require special software and post-processing equipment, which can add to the overall cost.
Relatively Slow:
Another challenge is that metal 3D printing is a relatively slow process. Unlike traditional machining processes, 3D printing builds objects layer by layer, often resulting in a slower overall production time. One of the main reasons that metal 3D printing is relatively slow is because each layer must be cooled before the next layer can be added. This cooling process is necessary to ensure that the layers bond correctly and do not warp or distort the final object.
Post-Processing:
Metal 3D-printed parts typically require post-processing to achieve the desired precision and accuracy. This may involve machining, heat treatment, or surface finishing, among other things. The post-processing step is essential to ensure that the final product meets the required specifications. In some cases, it may also be necessary to perform post-processing to improve the part’s strength or durability. Naturally, these extra steps take time and money.
How Can We Solve These Challenges of Metal 3D Printing?
Metal 3D printing is an exciting technology that shows great promise for the future. However, it also comes with its share of challenges. Here are three of the most common challenges of metal 3D printing and how to overcome them.
One of the biggest challenges of metal 3D printing is the high cost of materials and printers. One way to overcome this challenge is to use cheaper metals, such as aluminum or bronze. Another way to reduce the cost of metal 3D printing is to use less metal when printing objects. This can be done by using thinner metal layers or hollow objects. Also, as it becomes more popular, the overall cost of the printer is expected to decline.
Another challenge faced by metal 3D printers is the time required to print objects. Metal 3D printing is a slow process; it can take hours or even days to print a single object. This can be a problem for businesses that need to produce prototypes quickly or for individuals who want to print complex objects. One way to overcome this challenge is to use faster printers that are being developed. Another way to speed up the process is to use multiple printers working simultaneously.
In order to create a finished product, metal 3d printed parts must undergo a series of post-processing steps, including heat treatment, machining, and surface finishing. One way to overcome this challenge is to develop new post-processing technologies that are more efficient and effective. Additionally, new surface finishing techniques, such as cold spray coating, are being developed to give 3d printed parts a high-quality finish without the need for expensive machining operations.
By continuing to develop and improve associated technologies, we can make 3d metal printing more accessible and enable it to reach its full potential.
Leave a Reply