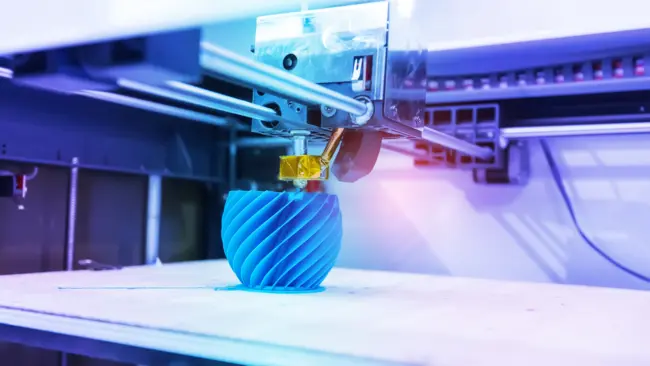
3D Metal Printing in Automotive Industry
As the automotive industry continues to grow and evolve, new manufacturing technologies are being developed to keep up with the demand for high-quality parts. 3D metal printing is one such technology that is gaining traction in the automotive market. Here we will take a closer look at what 3D metal printing is and how it is being used in the automotive industry.
What Is 3D Metal Printing?
When most people imagine a 3D printer, they think of plastic objects created from a template. However, technological advancements have made it possible for 3D metal printing to become a reality. In this process, metal powder is layered and fused using a high-powered laser beam. The resulting structure is strong and precise, requiring little to no post-processing. This technology offers benefits for both production efficiency and cost-effectiveness in industries such as automotive and aerospace manufacturing. As 3D metal printing continues to develop, it has the potential to revolutionize the way we approach product design and manufacturing.
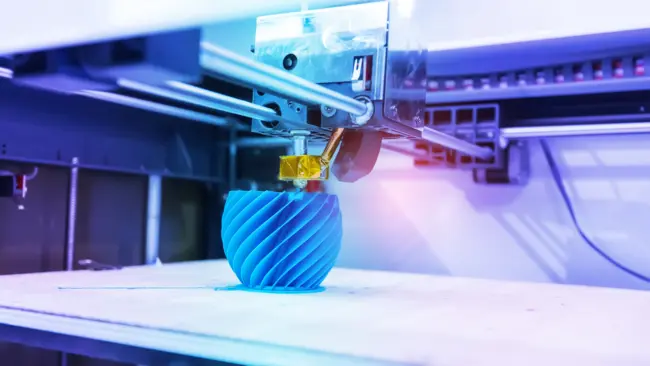
How Is 3D Metal Printing Used in the Automotive Industry?
The automotive industry has long been at the forefront of using advanced technology, from computer-aided design to robotics. One cutting-edge tool that is becoming more prevalent in automotive manufacturing is 3D metal printing, also known as additive manufacturing. As it is said before, this process involves building up layers of metal powder to create a finished product, allowing for greater flexibility and customization in design.
In the automotive industry, 3D metal printing has primarily been used for prototyping and small-batch production, as well as for creating complex engine parts and car body panels. The technology offers multiple benefits for the industry, including reduced manufacturing waste and cost savings through streamlined production processes. As 3D metal printing continues to advance, it is likely to play an even larger role in the future of automotive manufacturing.
Main Benefits of 3D Metal Printing in the Automotive Industry:
The automotive industry is constantly seeking new ways to improve efficiency and reduce costs, and 3D metal printing presents many opportunities in this regard. One benefit of this technology is the ability to produce complex parts with fewer steps, resulting in a streamlined production process. Additionally, 3D metal printing allows for customized and personalized designs that enhance performance and appeal to consumers. The decreased dependence on traditional manufacturing also means less waste and a smaller environmental impact. Overall, 3D metal printing offers exciting potential for the automotive industry in terms of cost savings, production efficiency, and innovative design possibilities. As this technology continues to advance, we can expect to see even greater benefits in the future.
Most Common 3D Metal Printed Products in the Automotive Industry:
The automotive industry has quickly embraced 3D metal printing to streamline production and create customized parts. Some common examples include turbocharger components, exhaust manifolds, and engine brackets. In addition, 3D metal printing allows for the creation of geometrically complex structures that were previously impossible to manufacture with traditional methods, such as heat exchangers and brake callipers. This technology also offers advantages in weight reduction, resulting in improved fuel efficiency and performance. As 3D metal printing becomes more widespread in the automotive industry, we can expect even greater design and functionality advances.
To Sum Up:
3D printing technology is revolutionizing the automotive industry. Metal-Tech offers a variety of metal 3D printers to help you get ahead in this rapidly changing market. With our years of experience, we can help you find the perfect printer for your needs and provide you with the support you need to make the most of this exciting new technology. Contact us today to learn more about how 3D metal printing can benefit your business!
Leave a Reply